
Landing Gears and Landing Gear Control Systems
Building on the confidence generated from years of experience in design, development, and manufacturing, SPP develops landing gear and landing gear control systems. The landing gear system is equipped with various control systems such as the main landing gear brake control system, nose wheel steering control system, and landing gear extension and retraction system. We continue to develop these systems to ensure even greater safety and reliability.
In the late 1990s, SPP was selected to provide to Goodrich the structural and actuation components in support of the landing gear systems for their CRJ700/900 series regional jets and in 2007 we began the development of the landing gear structural and actuation components for the latest CRJ1000 regional jets. With the experience gained from this project, we have evolved from a manufacturer of landing gear components to a company that designs, develops, and manufactures entire landing gear systems including peripheral systems such as the extension and retraction system and tail skid system.
Our comprehensive CATIA-based 3-D engineering capability and application of CAM/CAE systems enable us to undertake high-precision strength analysis, machining parts with complex design, and successfully prevent the mechanical interference and other problems in advance that can arise after installation on aircraft or during operation. We have also developed a very high strength stainless steel as an innovative material for landing gear and are continuing our research in the area of metal matrix composites and carbon-fiber composites.
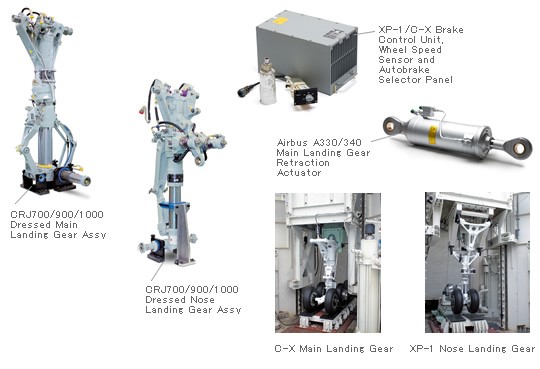
Our Activities in Research and Development
In order to realize a carbon-neutral society, we are conducting research and development of new technologies for aircraft electrification and weight reduction that contributes to higher energy efficiency of aircrafts.
Model-based development is being introduced to the research and development activities to pursue smart development with digitalization which intends higher quality, shorter lead times, and lower costs to enhance the total customer value.
Research & Development Theme
1. R&D of Electric Gear Pump & R&D of Electro-Hydraulic Actuator for Landing Gear Extension/Retraction System
2. R&D of Model Based Development techniques
R&D of Electric Gear Pump & R&D of Electro-Hydraulic Actuator of Landing Gear Extension/Retraction System
We are working in research to utilize an airborne electric gear pump for the aircraft central hydraulic source based on our gear pump technology, which is one of our strengths, to supersede the conventional piston-type, engine-driven pumps. On-demand hydraulic pressure supply to the aircraft hydraulic systems including flight control system and landing gear control system will contribute to the higher energy efficiency of aircrafts. The gear pump with its simple structure can also contribute to weight reduction, high reliability, and reduction of aircraft operating costs.
Electro-hydraulic actuators (EHA) is another application of the electric gear pump. We are engaged in research of EHA for the landing gear extension/retraction system having a dedicated electric gear pump(s) as the local hydraulic power source, to provide an optimal EHA for the landing gear control required at individual aircrafts. The research is in progress as a joint research with Airbus toward a next-generation electric aircraft.
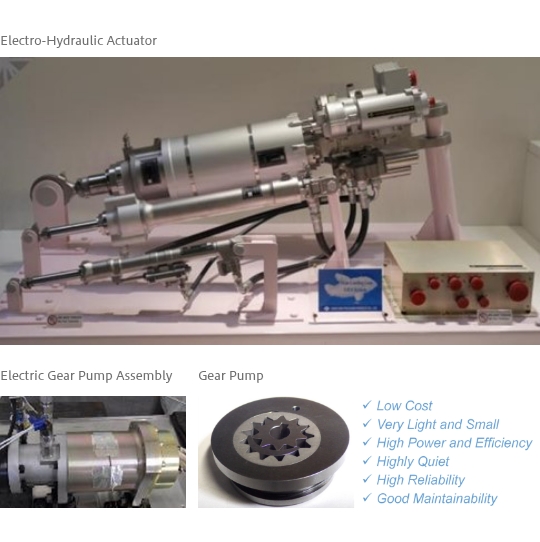
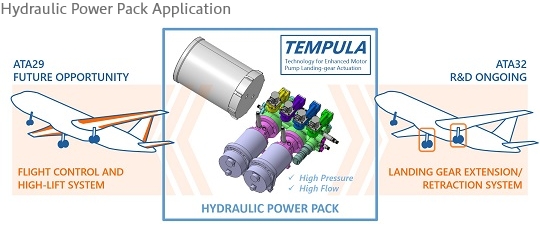
R&D of Model Based Development techniques
By performing a variety of computer simulation with system and component models, we have applied model-based development (MBD) to a series of design processes in the landing gear system development, including generation of component requirements, requirements validation and implementation verification.
In this research, we are proceeding with further studies on MBD application to our development in all aspects, such as establishment of Co-Simulation techniques combining independent simulations for control system analyses and structural analyses, replacement of 2D drawings with annotated 3D models, utilization of 3D models in manufacturing processes such as machining and inspection, application of additive manufacturing (AM) technology, application of automatic coding for software source code (ACG: Auto Code Generation) and evaluation through Hardware-In-the-Loop Simulator (HILS). These MBD techniques will make it possible to design optimal systems and components which support the aircraft electrification and contribute to the weight reduction toward the carbon-neutral society.
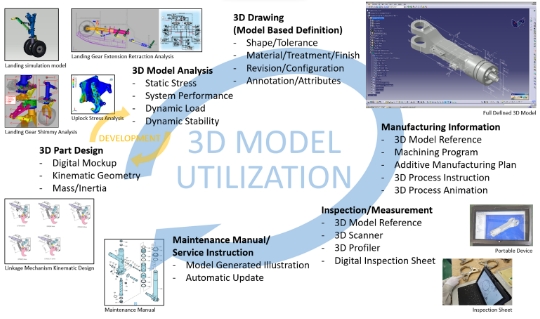